A Topological Approach to Preventive Maintenance and Causation Monitoring
Sustaining Industrial Equipment
The industrial sector depends heavily on the reliability and longevity of its equipment. Downtime and failures are not just inconveniences; they can be costly and even dangerous. Wingenium’s advanced Topological Data Analysis (TDA) algorithms provide an innovative solution for sustaining industrial equipment through preventive maintenance and causation monitoring.
Preventive Maintenance of Heavy-Duty Equipment
Preventive maintenance is critical for the health and operational longevity of heavy-duty machinery. Wingenium’s TDA-based solutions take a proactive stance in this maintenance regime.
Multidimensional Equipment Health Monitoring
Wingenium utilizes TDA to model the multidimensional data generated by heavy-duty machinery sensors. By creating topological models of normal operating conditions, we can identify deviations that signal wear and tear or potential failures. This allows for maintenance schedules to be optimized, ensuring machinery is serviced precisely when needed, avoiding both unnecessary maintenance and unexpected breakdowns.
Predictive Failure Detection
Persistent homology is particularly effective in predicting equipment failure. It analyzes the machinery's sensor data over time to detect topological changes, which often precede a failure. By tracking these topological “signatures,” Wingenium can forecast potential issues before they lead to costly downtime, enabling maintenance crews to address problems early.
Causation Monitor for Mission-Critical Machinery Failures
For mission-critical machinery, understanding the causation of failures is essential to prevent recurrence and maintain operational integrity.
Complex Causation Modeling
Wingenium’s TDA approach models the complex interactions within machinery data that contribute to failures. By examining the persistent features in the topological space of operational data, we can trace back the causal factors leading to a failure, even in seemingly random or stochastic systems.
Real-Time Monitoring and Alerting
Our TDA solutions offer real-time monitoring capabilities. By constantly analyzing the topological structure of sensor data streams, Wingenium’s algorithms can instantly detect anomalies and provide alerts, facilitating immediate action to prevent machinery failure.
Implementing Wingenium’s TDA Solutions in Industrial Equipment Maintenance
Wingenium’s solutions are tailored to integrate with the industrial sector's existing data infrastructure. Our algorithms are scalable, designed to handle vast arrays of sensor data from diverse machinery
Interactive Topological Data Maps
Wingenium provides interactive topological data maps that enable maintenance personnel to visualize the health and performance of their machinery intuitively. These maps are a powerful tool for interpreting complex sensor data and making informed decisions about equipment maintenance.
Extensive Training and Support
Understanding the intricacies of TDA and its application in industrial contexts is vital. Wingenium offers comprehensive training and support to ensure that maintenance teams can fully leverage the predictive power of TDA in their preventive maintenance strategies.
Summary
In an industry where the stakes are high, and the machinery is complex, Wingenium’s TDA-based solutions provide a cutting-edge approach to preventive maintenance and causation monitoring. By oIering a deeper understanding of the topological data structures underlying equipment operation, Wingenium empowers industrial enterprises to maintain their machinery eIectively, ensure safety, and optimize their operations for the long haul.
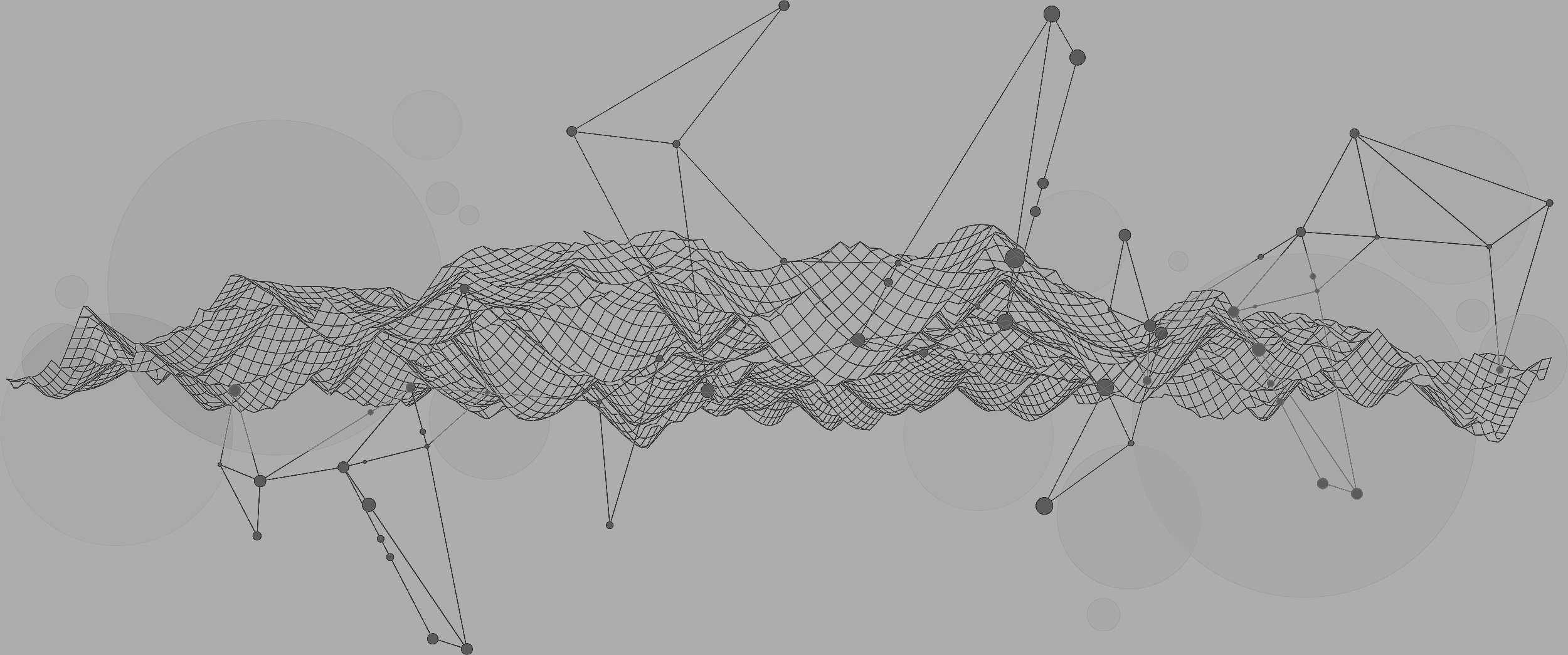
Would you like more information?
If you want to more information about this subject please get in touch with our Topology expert, who would be pleased to hear from you.
Invoke Ingenuity Data Topology Specialist
Ingenuity Framework is designed and maintained by our Data Topology team who are backed by our R&D on TDA sciences.