Productization Pathways
Insights
Productization Pathways for Predictive Maintenance in Manufacturing Industry
Predictive and importantly, preventive maintenance is a game-changer. It empowers manufacturers to shift from a reactive maintenance approach to a proactive one, significantly reducing downtime, improving productivity, and ultimately, boosting the bottom line. However, taking predictive maintenance from an idea to a tangible, scalable product is a journey that involves several critical pathways
The Essence of Predictive Maintenance
Predictive maintenance relies on data analytics and machine learning to predict equipment failures before they occur. By monitoring the condition of machinery and analyzing data, manufacturers can identify anomalies, detect early signs of deterioration, and schedule maintenance tasks precisely when needed. This approach replaces the traditional "fix it when it breaks" mindset, saving both time and resources.
Technical Example: Suppose you have a fleet of CNC machines. Each machine generates sensor data, such as temperature, vibration, and current consumption. You need to collect this data in real-time and integrate it into a central data repository for analysis.
Real-life Use Case: Schlumberger implemented a predictive maintenance solution that collects data from drilling equipment to optimize drilling operations and prevent costly equipment failures.
Pathway 1: Data Acquisition and Integration
The foundation of any predictive maintenance solution is data. Manufacturers must gather data from various sources, including sensors, industrial IoT devices, SCADA systems, and historical maintenance records. This data comes in different formats, frequencies, and structures, making data integration a critical first step.
Technical Example: You have data from a pressure sensor that occasionally produces spikes due to measurement errors. To preprocess the data, you apply filters to remove outliers and smooth the time series.
Real-life Use Case: Siemens employs data preprocessing techniques to analyze data from train sensors and predict maintenance needs, ensuring railway networks run smoothly.
Pathway 2: Data Preprocessing and Cleaning
Raw data from industrial environments is often noisy and unstructured. Data preprocessing involves cleaning, transforming, and structuring the data to make it suitable for analysis. This step is crucial for improving the accuracy of predictive models.
Technical Example: For an industrial pump, you engineer features like mean vibration amplitude, peak temperature, and energy consumption overtime intervals.
Real-life Use Case: General Electric's (GE) Predix platform leverages feature engineering to analyze data from jet engines, enabling airlines to predict engine failures and optimize maintenance schedules.
Pathway 3: Feature Engineering
Feature engineering involves selecting and creating relevant features (attributes) from the data that capture the characteristics of the machinery's condition. Effective feature engineering enhances the performance of machine learning models.
Technical Example: You train a Random Forest classifier to predict the remaining useful life (RUL) of an industrial motor based on features like temperature and vibration.
Real-life Use Case: Rolls-Royce employs deep learning models to analyze data from aircraft engines and predict component failures.
Pathway 4: Machine Learning Model Development
Machine learning models lie at the core of predictive maintenance. These models use historical data to identify patterns and make predictions about when equipment is likely to fail. Common algorithms include regression, decision trees, and deep learning.
Technical Example: You develop an API that exposes the predictive maintenance model, allowing real-time predictions to be made from within the SCADA system.
Real-life Use Case: Tesla integrates predictive maintenance models into its electric vehicle (EV) manufacturing process, optimizing the maintenance of robotic assembly lines.
Pathway 5: Deployment and Integration
Once you have a trained model, the next step is deploying it in the production environment. Integration with existing systems, such as supervisory control and data acquisition (SCADA) systems, ensures seamless operation.
Technical Example: You set up a monitoring system that triggers model updates when prediction accuracy drops below a certain threshold.
Real-life Use Case: ABB uses continuous monitoring to keep its predictive maintenance models up to date, ensuring the reliability of its industrial robots.
Pathway 6: Continuous Monitoring and Model Updates
Predictive maintenance is not a one-time implementation; it's an ongoing process. Continuous monitoring of model performance and data quality is crucial. As equipment and data patterns change, models need regular updates.
Technical Example: You create a web-based dashboard that displays equipment health scores and RUL predictions. Maintenance personnel receive SMS alerts when critical equipment requires attention.
Real-life Use Case: IBM Watson IoT offers an industrial equipment maintenance solution with a user-friendly interface and alerting system.
Pathway 7: User Interface and Alerts
For predictive maintenance to be effective, it needs to provide actionable insights to maintenance teams. User interfaces and alerting systems enable users to visualize predictions and receive timely notifications.
Technical Example: You deploy a distributed computing solution that can process data from hundreds of sensors across multiple factories.
Real-life Use Case: Honeywell scales its predictive maintenance solution to cover entire refineries, helping customers prevent unplanned downtime and reduce maintenance costs.
Pathway 8: Scaling and Optimization
As predictive maintenance proves its value, manufacturers often seek to expand its application to more equipment and facilities. Scaling involves optimizing data pipelines, models, and infrastructure to accommodate larger datasets and increased computational demands.
Productizing predictive maintenance in the manufacturing industry requires traversing multiple technical pathways. It involves collecting and preprocessing data, engineering meaningful features, developing machine learning models, deploying them into production environments, and continually monitoring and improving their performance. Real-life use cases from industry leaders demonstrate the transformative potential of predictive maintenance in manufacturing.
By following these pathways and embracing the power of predictive maintenance, manufacturers can not only reduce operational costs but also achieve higher production efficiency and superior product quality. In an era where data-driven decisions are paramount, predictive maintenance serves as a beacon of innovation, guiding the manufacturing industry toward a more efficient and sustainable future.
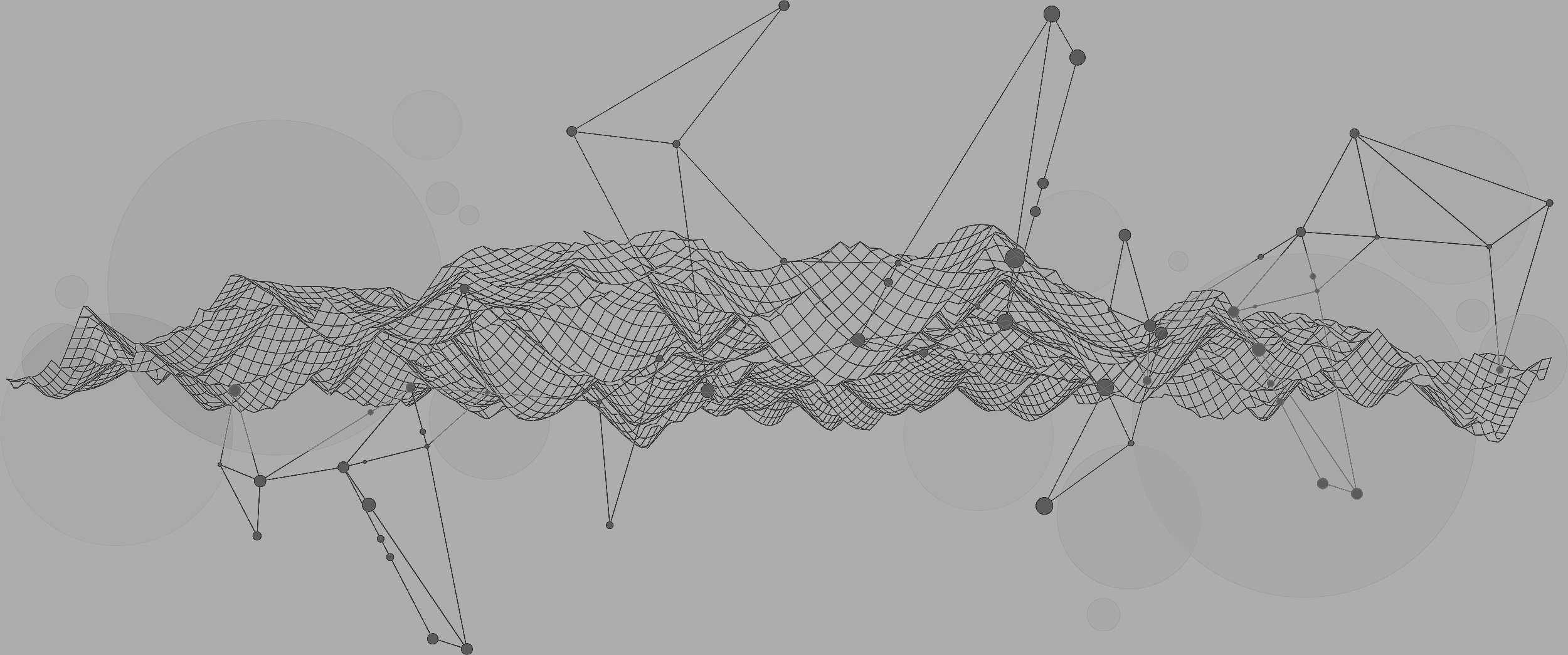
Would you like more information?
If you want to more information about this subject please get in touch with our Topology expert, who would be pleased to hear from you.
Invoke Ingenuity Data Topology Specialist
Ingenuity Framework is designed and maintained by our Data Topology team who are backed by our R&D on TDA sciences.